A winch 50 ton, a workhorse in heavy lifting and pulling applications, demands meticulous maintenance to ensure its optimal performance, safety, and longevity. Whether used in construction, mining, or marine operations, regular maintenance is essential to prevent wear and tear, minimize downtime, and extend the lifespan of this critical equipment. In this comprehensive guide, we will delve into key aspects of maintaining a winch 50 ton, providing insights into best practices and strategies for effective upkeep.
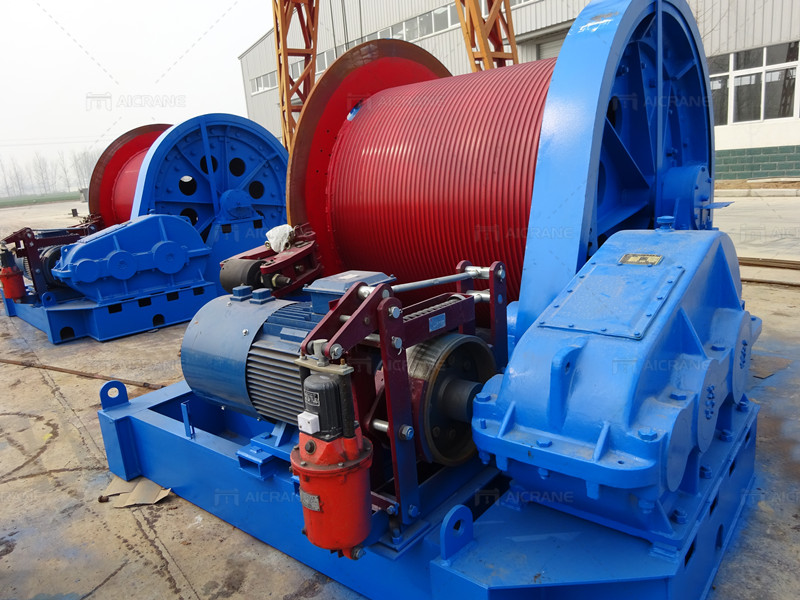
Inspection and Lubrication
Routine inspections are the cornerstone of winch maintenance. Regularly examine all components of the winch, paying close attention to the wire rope or cable, drum, gearbox, and motor. Look for signs of wear, corrosion, or damage. Inspect the wire rope for broken strands, kinks, or deformities, and replace any compromised sections promptly. Additionally, check the drum for any irregularities and ensure it is properly aligned.
Lubrication is crucial for the smooth operation of the winch. All moving parts, including bearings, gears, and the drum, should be adequately lubricated. Choose a lubricant suitable for the environmental conditions and load capacities of the winch. Regularly grease fittings and pivot points, following the manufacturer’s guidelines on lubrication intervals. Proper lubrication not only reduces friction but also protects against corrosion, contributing to the overall efficiency and longevity of the winch.
Electrical System Check
In the case of electric winches, the electrical system is a critical component that requires regular inspection. Examine the wiring, connections, and control systems for any signs of wear, corrosion, or loose connections. Ensure that the control panel is clean and free from debris, and check that buttons and switches operate smoothly.
Electrical components are susceptible to environmental factors, so it’s essential to protect them from moisture, dust, and other contaminants. Regularly clean and inspect electrical enclosures, and consider using protective covers or housing to shield sensitive components from adverse conditions.
Brake System Inspection
The brake system is a vital safety feature in any winch. Regularly inspect the braking mechanism to ensure it is functioning correctly. This includes checking brake pads or shoes for wear and adjusting the brake if necessary. If the winch is equipped with an automatic brake system, ensure that it engages and disengages appropriately.
In the event of any issues with the braking system, address them immediately. Failure to maintain a reliable brake system poses a significant safety risk during lifting and lowering operations.
Gearbox and Transmission
The gearbox and transmission system are integral to the performance of the winch. Regularly check for oil leaks around the gearbox and inspect the oil level according to the manufacturer’s recommendations. Change the gearbox oil at specified intervals to ensure optimal lubrication and prevent premature wear.
Examine gears for signs of wear, chipping, or misalignment. Any abnormalities in the gearbox can lead to decreased efficiency and increased stress on the winch components. Timely maintenance of the gearbox is crucial to prevent costly repairs and ensure the longevity of the winch.
Load Testing and Calibration
Periodic load testing is essential to verify the winch’s capacity and performance. Conduct load tests within the specified limits to ensure the winch can handle its rated load safely. During load testing, observe the winch’s response to various loads, checking for any unusual noises, vibrations, or performance issues.
Calibrate the winch’s load monitoring system regularly to ensure accurate readings. This is particularly important for applications where precise load control is critical. Regular calibration helps maintain the winch’s accuracy and ensures that it operates within safe parameters.
Environmental Considerations
The environment in which the winch operates significantly influences its maintenance needs. In harsh or corrosive environments, such as marine or industrial settings, additional precautions are necessary. Regularly clean the winch to remove accumulated dirt, salt, or other corrosive substances. Apply protective coatings or treatments to vulnerable components to guard against corrosion.
Consider the use of environmental seals or covers for critical components to shield them from adverse weather conditions. Protective measures tailored to the specific environmental challenges faced by the winch enhance its resilience and contribute to long-term reliability.
Operator Training and Awareness
Proper maintenance extends beyond physical inspections; it also involves operator training and awareness. Ensure that operators are well-trained in the correct operation of the winch, including the use of safety features and emergency procedures. Promote a culture of proactive reporting, encouraging operators to notify maintenance personnel of any unusual sounds, vibrations, or performance issues promptly.
Regularly review and update operator manuals and provide ongoing training to keep operators informed about the latest maintenance practices and safety protocols. Well-informed operators contribute to the overall reliability and safety of the winch.
In conclusion, maintaining a winch 50 ton requires a comprehensive and systematic approach. Regular inspections, lubrication, attention to electrical systems and brakes, gearbox maintenance, load testing, consideration of environmental factors, and operator training are all integral to ensuring the winch’s optimal performance and longevity.
A well-maintained winch not only enhances operational efficiency but also minimizes the risk of breakdowns and accidents. Establishing a proactive maintenance schedule, adhering to manufacturer recommendations, and addressing issues promptly are essential practices for any organization relying on the consistent and reliable performance of a <a href=“https://aicranemachine.com/50-ton-winch/”> winch 50 ton</a> in heavy lifting and pulling applications.

Comments
No comments yet. Be the first to react!